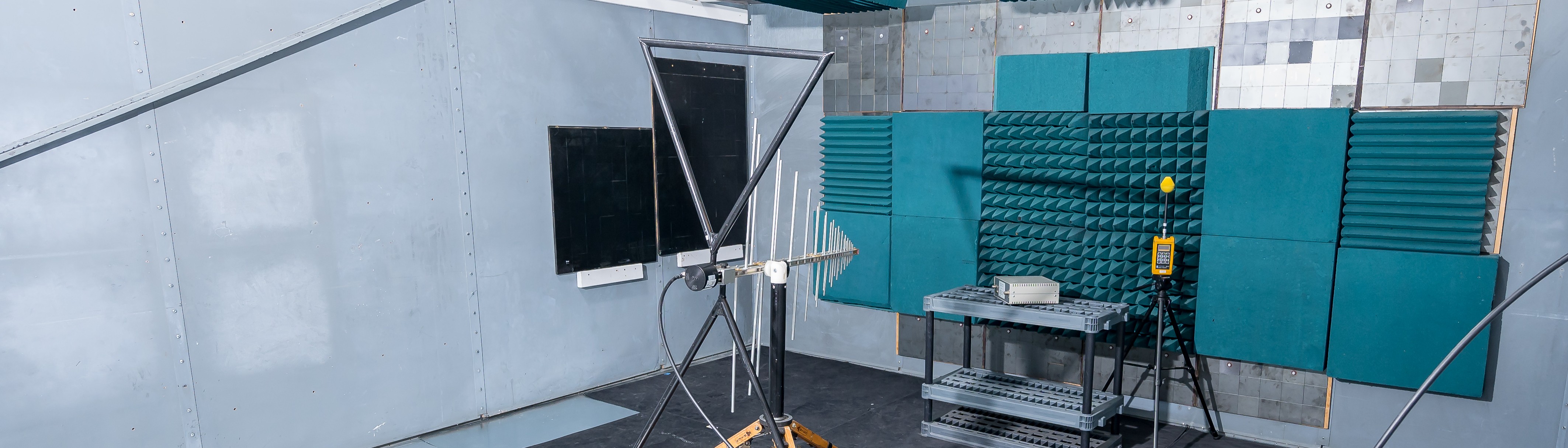
Demystifying EMC and Product Testing: 10 FAQs & Expert Answers
Question 1: What is the purpose of EMC testing?
Answer: EMC (Electromagnetic Compatibility) testing ensures that an electronic device doesn’t emit an excessive amount of electromagnetic interference (EMI) and is robust enough to operate as intended in its electromagnetic environment. It ensures that products can coexist without interfering with the operation of other products and comply with regulatory standards. Learn more about the difference between EMI and EMC.
Question 2: How can we determine which EMC standards apply to our product?
Answer: Identifying applicable EMC standards depends on various factors: the type of product, its intended use and the geographical markets where it will be sold. Often, regulatory bodies and industries in different regions (like the EU and USA) have distinct standards, such as CE and FCC. Consulting with an EMC expert or testing lab will help tailor testing to your specific product and target market.
Question 3: What is the difference between pre-compliance and full-compliance testing?
Answer: Pre-compliance testing is an initial stage, utilized to identify potential EMC issues early in the design phase, often using simplified setups. Full-compliance testing is a formal process, adhering strictly to regulatory standards, and is typically conducted in a certified laboratory environment to ensure the product meets all applicable EMC requirements for market release.
Question 4: How long does EMC testing generally take?
Answer: The duration of EMC testing can vary widely based on the product complexity, number of tests required, and the applicable standards. Typically, testing may range from a few days to several weeks. Scheduling, lab availability, and any re-testing (if issues are identified) can also influence the timeline.
Question 5: What should we provide for the EMC testing of our product?
Answer: At least one sample to be tested, a backup sample if possible and any support equipment necessary for the sample operation (e.g. a laptop with software that can communicate with the sample, instructions on how to use the product and any precautions to be observed while using the product). A lab may ask for drawings and schematics if they are trying to help a manufacturer solve an EMI problem.
Question 6: How can we mitigate potential failures or delays in EMC testing?
Answer: Early engagement with the testing laboratory and conducting pre-compliance testing can identify potential issues early on. Ensuring your design adheres to best practices in EMC design, such as proper shielding, filtering, and layout, can also mitigate the risk of failures during the final compliance testing.
Question 7: How are EMC testing results documented and reported?
Answer: EMC testing results are documented in a detailed technical report, which includes information like the product description, test procedures, configurations used, test environments, and, of course, the test results. Photographs and diagrams accompany text to provide a thorough depiction of the testing conditions and setups.
Question 8: Can EMC testing be performed in-house?
Answer: While it is possible to conduct some level of EMC testing in-house, especially during the development stages (pre-compliance testing), for regulatory approval, full compliance testing needs to be conducted by an accredited laboratory to ensure that all applicable standards and regulations are strictly adhered to.
Question 9: If a product fails EMC testing, what are the next steps?
Answer: If a product fails EMC testing, it’s crucial to conduct a thorough analysis of the test data and work closely with EMC engineers to identify the root cause of the failure. Subsequent steps may involve redesigning certain aspects of the product and then re-testing to validate the solutions implemented.
Question 10: How can we ensure our product remains compliant with EMC standards post-launch?
Answer: To ensure ongoing compliance, it is crucial to implement a robust change management process, where any modifications to the product including components, layout and software are assessed for their impact on EMC performance. Periodic re-testing or spot-checking of products, especially if substantial changes have been made, will also help assure continued compliance.
In Conclusion
Engaging with EMC experts throughout the product lifecycle, from design through to production, can ensure both efficient and effective navigation through the complexities of EMC compliance.
Contact us today to get started.