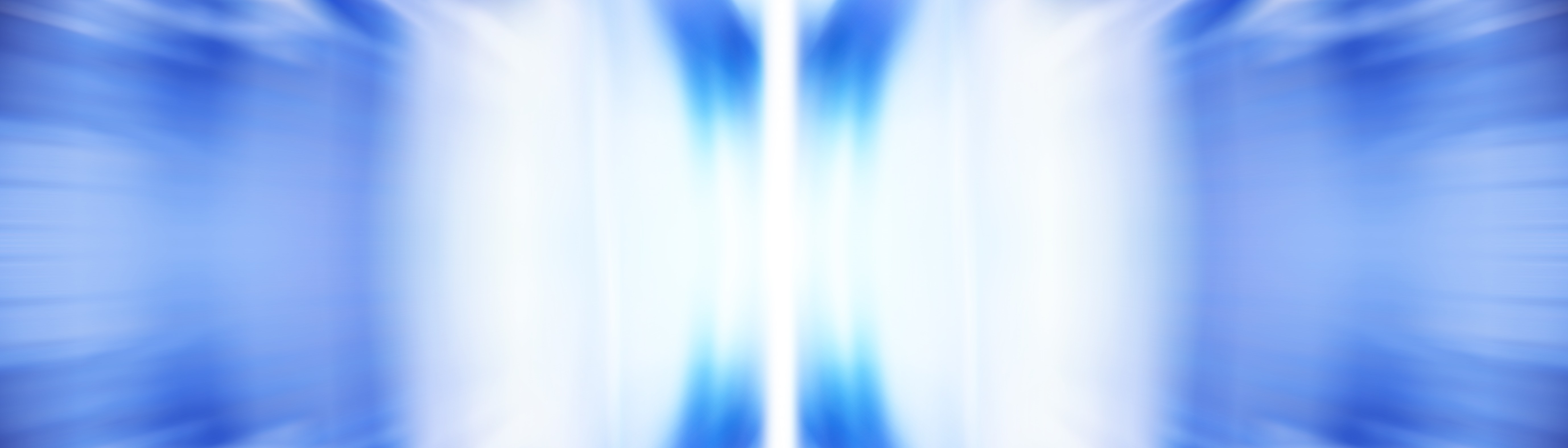
Debunking Common Myths about Product Safety Testing
Testing electronic products for safety is an essential part of bringing them to market. This could include testing for compliance with CE (Conformité Européenne).
There are a lot of misconceptions out there when it comes to product safety testing. Let’s take a look at a few of the most common myths and debunk them.
Myth 1: Product Safety Testing is Too Expensive
Product safety testing can seem like a daunting task, but it doesn’t have to be expensive. With the right preparation, planning and guidance, you can minimize the cost and make testing work for your budget.
It’s important to note that some regulations require a third-party professional to conduct a valid product safety test.
If you are a manufacturer conducting tests on your own, make sure you know what type of test equipment will be required and how much time it will take to complete the tests.
If you need CE Mark for your product, consider working with a reputable laboratory that can guide you through the entire process in an efficient and cost-effective manner.
Without a doubt, having a valid certificate of conformity will save you money in the long run as it will protect you from incurring fines or other penalties for non-compliance with current regulations.
Myth 2: Product Safety Tests Take Too Long
The length of time it takes to complete a product safety test depends on several factors including the complexity of the device being tested and whether or not all aspects of the testing have been adequately prepared in advance.
In many cases, if proper preparation has been handled beforehand, it is possible to reduce the amount of time needed for product safety tests significantly without sacrificing accuracy or quality.
By taking advantage of pre-compliance options such as preliminary assessments prior to beginning full compliance tests, you can drastically reduce your overall turnaround times while still ensuring your products meet all necessary regulatory requirements.
Myth 3: Compliance is a set-it-and-forget-it type of deal
It is true that once your product is certified, you can bring it to market with confidence. Keep in mind there are instances that might necessitate further proof of compliance of your product. For example, as changes to your product design are made, or as standards change, your product might require further approval.
Design iteration is a key ingredient for innovation. To ensure that you are maintaining compliance throughout your product’s evolution, review the applicable guidelines and reach out to your laboratory with any questions.
The Truth About Product Safety Testing
- Meeting regulatory requirements is cost-effective.
- Proper preparation can expedite the testing process.
- There are instances where you may need additional approval for your product post-launch.
Working with an accredited laboratory will guide you smoothly through the process. With the proper planning, preparation and testing services you will eliminate the risk of suffering expensive penalty fees and headaches for not meeting compliance.
GME is here to help
Green Mountain Electromagnetics is an ISO 17025-accredited laboratory that tests for product compliance with CE standards.
With 30 years in the industry, our team of experts is equipped with the latest technology and knowledge to ensure reliable test results. GME is A2LA accredited and supports clients, developing long-term business relations.
Contact us today to find out more about our services!